Reasons
The main reasons for additional marking of the products are:
- Easy and quick distinguishing of individual pieces of equipment which supplements the unique marking done by the manufacturer. In such case the user can mark the equipment as needed, while observing the basic conditions. See below.
- Adding marking for the purposes of recording the periodic inspection performed. In such case the user can mark the equipment as needed, while observing the basic conditions. See below.
- Renewing the damaged original marking of the manufacturer, which may have become illegible due to wear. In this case it is absolutely necessary to respect the original marking method, so that the data entered by the manufacturer during the manufacturing process are not altered. This marking must be performed before the original information is lost.
- Creating your own system of unique numbers for the products that do not have their unique numbers from the manufacturing process. This task should be undertaken by a competent person who establishes the system of marking which prevents duplications and allows to track the individual product items throughout their lifetime. This system must be established on the day of starting of using the product at the latest.
Conditions
Additional marking can be done to achieve better organization and tracking of your Singing Rock equipment. This marking must comply with the following conditions:
- Additional marking must not alter or cover the original marking of the Singing Rock manufacturing company.
- The method used must not damage your equipment significantly, making it unfit for further use.
- The selected method of marking must not damage other equipment which comes in contact with the marked equipment, either.
- Any marking may damage your equipment, therefore place your mark carefully in order to avoid damage as much as possible.
- In case of creating unique marking of products that are not distinguishable in any other way, the person performing this activity is responsible for the uniqueness of the marking and the correct recording of the information in the registration system.
Choose the place for marking following the sequence below:
- Places designated for marking by the manufacturer.
- The parts of the product which do not have supporting function.
- The most solid parts of the product whose slight damage will not have any impact.
Suitable Marking Methods
The Singing Rock Permanent Marker (SR Permanent Marker)
Advantages:
- Suitable for marking the textile when other methods cannot be used (for example marking a half of a rope).
- Does not impact the load bearing capacity of the marked product.
Disadvantages:
- Can only be used on absorbent materials – textile.
- Is black and therefore may be mistaken for other kinds of chemical damage.
- May seep through to the opposite side of the label and turn the manufacturer’s information illegible, which eventually results in discontinuing the use of the product.
- Legibility of the record may be limited.
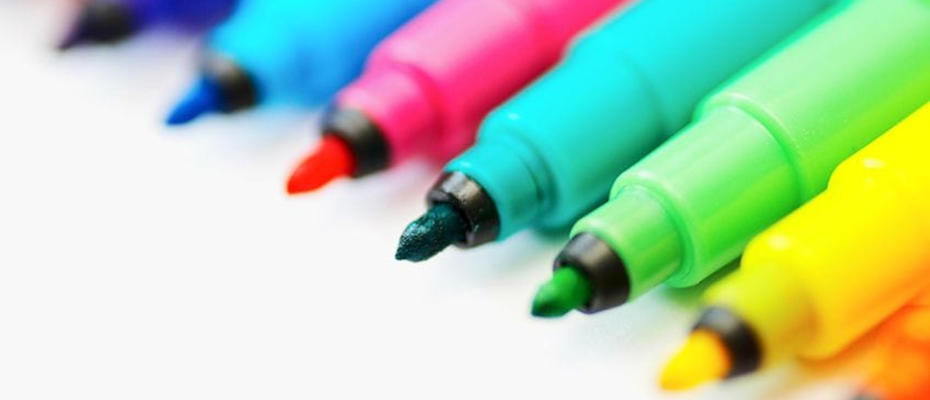
Lacquer pens for metal
Advantages:
- Suitable for marking the metal equipment.
- Good legibility of the record.
Disadvantages:
- Worse durability of the record.
- Can only be used on metal material.
- Worse long-term colour permanence.
- It can contaminate textile during application..
Alcohol permanent marker (A permanent marker)
Advantages:
- Good legibility of the record.
- Easily available.
- Easy manipulation.
Disadvantages:
- Cannot be used on the load bearing textile parts of the product. Given that the Singing Rock company cannot test the impact of all the markers available in the market, such contamination is considered a chemical damage to the product and the product must not be used any longer.
- Is not suitable for marking the strength plastic parts, such as helmet shells etc.
- May seep through to the opposite side of the label and turn the manufacturer’s information illegible, which eventually results in discontinuing the use of the product.
- Degradation caused by UV radiation.
- Unstable on the metal material – may spread to textile and cause its contamination.
Engraving to the depth of up to 0,1 mm
Advantages:
- Good legibility of the record.
- Good durability.
Disadvantages:
- Cannot be used on textile and plastic products.
- May mechanically damage the product. Especially the small parts, friction segments, rivets.
Stickers and sticking labels, adhesive tapes.
Advantages:
- Easy application.
- Good legibility of the record.
Disadvantages:
- Low durability.
- Possible contamination of equipment with glue.
- Not suitable for textile.
- Unsuitable Marking Methods:
Unsuitable Marking Methods:
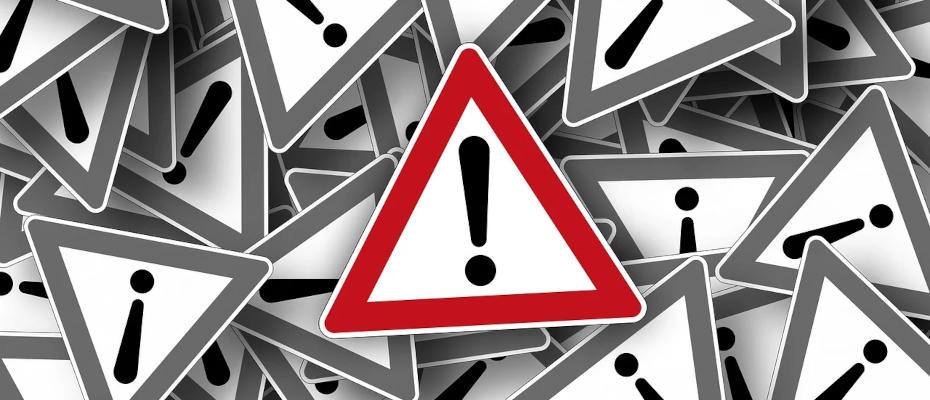
The following methods permanently and irreversibly damage equipment or change its properties. The seriousness of such damage is hard to determine, therefore the following methods are NOT recommended:
- embossing with dies
- branding
- etching
- cutting
- stitching marks on the equipment
- bending
Recommended Marking Methods Based on Type of Material
Harnesses
The marking is done:
- On the places designated for marking, which can be found on the label and sometimes also on the shoulder strap. The marking should be done using the A permanent marker or a suitable sticker.
- It should be carried out on the padding and reinforcements whose slight damage does not have impact on functioning or load bearing capacity of the harness. The marking should be done with an alcohol permanent marker or the SR Permanent Marker. A sticking label can be used on suitable places.
- On the load bearing straps of the harness. Marking can only be carried out using the SR Permanent Marker.
Ropes
Ropes are marked from manufacture; additional marking is done using:
- Sticking labels containing information on the year of manufacture, type of the rope, length, manufacturer and unique number. To increase its durability the label can be covered by a shrinking tube with glue.
- SR Permanent Maker can be used to mark the middle of the rope.
- A chip can be used on the ends of the rope, but this kind of marking is difficult as for the equipment needed both during application and outdoors.
Each rope has a unique number from manufacture, however, during its use its length may change, therefore the details in the label may not correspond to reality. In such case it is necessary to establish your own marking system, but only if the original marking of the rope can be traced back.
Example:
There is a 100m-long rope with product number 12345. During its use the rope is divided into two 50 m parts. The resulting ropes can be marked 12345/A and 12345/B. If we cut the 12345/A rope, the resulting ropes are marked 12345/A/1 and 12345/A/2.
The format of the marking is not as important as the continuity and possibility to track the original rope in the history of changes and periodic inspections.
Slings
Slings are marked from manufacture by a label. An own record can be entered on this label provided that the information entered by the manufacturer remains legible. The marking is done:
- On the clear part of the label with an A permanent marker. We ensure that the marker does not seep to the side of the label with information from the manufacturer, making it illegible.
- Also, an identification sticker label can be put on the clear side of the label.
- The textile can be marked directly by the SR Permanent Marker.
- If a sling has parts that do not have load bearing function (such as rope protector), an alcohol permanent marker can be used for marking..
Helmets
Helmets are usually equipped with an identification label stuck to the inner side of the shell. The marking is done as follows:
- We make our own mark on the identification label with an A permanent marker. The original information provided by the manufacturer must remain legible.
- Our own sticking labels can be put on parts of the shell specified in the Instructions for Use of the helmet. The glue of certain labels can be aggressive. It is recommended to put such labels on stickers provided with the helmet by the manufacturer.
- The SR Permanent Marker can be used on the straps of the helmet’s fastening system..
Carabiners
Additional marking can be carried out on carabiners provided that it does not limit their function and legibility of the original information from the manufacturer:
- By a lacquer pen for metals. Alternatively, nail polish can be used. The colour must be sufficiently durable, must not disrupt the structure of the metal and cannot spread to the textile material which may come into contact with it. Roughened surface of the lock nut and recesses on the carabiner body are suitable for placing the marking.
- By engraving, provided that the maximum depth of engraving will not excess 0,1 mm. Screw locks, body of the carabiner next to the date of manufacture or the metal mechanism of the action opening system of the hook carabiners are suitable for placing the marking.
- Sticking labels and coloured adhesive tapes should be placed on the less exposed parts of carabiners and in case of accidental removing of the tape we should prevent spreading of the glue on the textile material..
The places unsuitable for placing the marking are: joints, rivets, spring, nose and gate of the carabiner and the places most exposed to contact with other material.
Other metal material
Other metal material, such as pulleys, rappel devices, ascenders, fall arresters, rigging plates and complex devices are marked as follows:
- Sticking labels and coloured adhesive tapes should be placed on the less exposed parts and in case of accidental removing of the tape we should prevent spreading of the glue on the textile material. This method is especially suitable for larger and complex products (retractable fall arresters, tripods, etc.)
- By a lacquer pen for metals. Alternatively, nail polish can be used. The colour must be sufficiently durable, must not disrupt the structure of the metal and cannot spread to the textile material which may come into contact with it.
- By engraving, provided that the maximum depth of engraving will not excess 0,1mm. The suitable places for markings are the sides of rappel devices, side plates of pulleys and fall arresters, bodies of ascenders and rigging plates.
Unsuitable marking points are the contact surfaces of the friction segments of the rappel devices and fall arresters, and pulley sheaves!.
FAQ
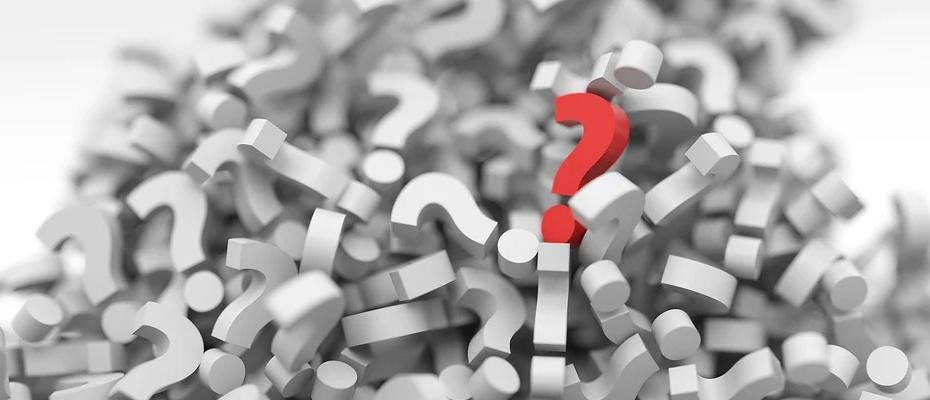
Can I duplicate the unique marking of the manufacturer in case it is completely or partially illegible? (Such as illegible numbers on carabiners.)
Yes, if we are sure which product this is and we know its history. This means we should do this as a precaution, so that products cannot be mutually confused. Throughout its lifetime the history of the product must be continually tracked. The person who performs marking must be competent, must be listed in the periodic inspection report or in the record sheet and is responsible for the accuracy of the created data.
Can I create my own marking if the original marking was lost? (For example, if the label is missing on the sling or on the helmet.)
In such case: NO, this product is not complete and is not in the condition in which it was approved by the testing institution. All the labels are integral part of the product, and the product must not be used without them.
Can I create my own marking if the product has never been marked?
In such case it is necessary to create your own marking to be able to track the product throughout its use. The person who performs marking must be competent, must be listed in the periodic inspection report or in the record sheet and is responsible for the accuracy of the created data.